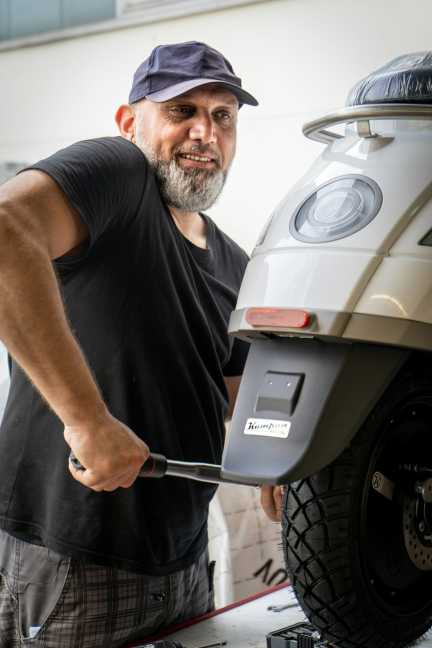
The importance of continuous improvement in production processes
Share0In today’s fast-paced and competitive business environment, the importance of continuous improvement in production processes cannot be overstated. With technological advancements and changing consumer preferences, companies must constantly adapt and evolve their processes to remain competitive and profitable.
Continuous improvement, or Kaizen as it is known in Japanese, is a philosophy that emphasizes the importance of making small, incremental changes to improve efficiency and effectiveness in production processes. By fostering a culture of continuous improvement, companies can reduce waste, increase productivity, and ultimately enhance their bottom line.
One of the key benefits of continuous improvement in production processes is the identification and elimination of waste. Waste can take many forms in a production process, including excess inventory, defects, and unnecessary processing steps. By continuously analyzing and improving processes, companies can identify and eliminate waste, thereby reducing costs and improving overall efficiency.
Another benefit of continuous improvement is increased productivity. By making small changes to streamline processes and eliminate unnecessary steps, companies can improve productivity and increase output without increasing costs. This can lead to significant cost savings and improved competitiveness in the marketplace.
In addition to reducing waste and increasing productivity, continuous improvement can also lead to improved quality. By constantly monitoring and analyzing processes, companies can identify areas where quality issues may arise and take proactive steps to address them. This can lead to fewer defects, higher customer satisfaction, and ultimately, increased profitability.
Continuous improvement is not just about making changes for the sake of change. It requires a systematic approach to process improvement that involves setting clear goals, measuring performance, and constantly seeking ways to improve. This often involves engaging employees at all levels of the organization and encouraging them to contribute ideas and solutions for process improvement.
One of the key components of successful continuous improvement initiatives is the use of data and analytics. By collecting and analyzing data on key performance indicators, companies can identify trends and patterns in their processes and make informed decisions about where to focus their improvement efforts. This data-driven approach can help companies prioritize their improvement efforts and ensure that they are making the most impactful changes to their processes.
Continuous improvement is not a one-time event, but rather an ongoing process that requires commitment and dedication from all members of the organization. It requires a willingness to challenge the status quo, take risks, and experiment with new ideas. It also requires a culture of accountability, where employees are encouraged to take ownership of their work and strive for continuous improvement in everything they do.
In today’s rapidly changing business environment, companies that fail to embrace continuous improvement risk falling behind their competitors. By constantly seeking ways to improve their processes, companies can stay ahead of the curve and ensure their long-term success.
One industry that has embraced continuous improvement in production processes is the automotive industry. Companies like Toyota have long been leaders in the use of Kaizen and other continuous improvement techniques to drive efficiency and quality in their production processes. By constantly seeking ways to eliminate waste and improve productivity, these companies have been able to maintain their competitive edge and continue to grow their market share.
In conclusion, the importance of continuous improvement in production processes cannot be overstated. By constantly seeking ways to eliminate waste, increase productivity, and improve quality, companies can stay competitive and profitable in today’s fast-paced business environment. The key to success lies in fostering a culture of continuous improvement and empowering employees at all levels to contribute to the process. By embracing continuous improvement, companies can drive efficiencies, reduce costs, and ultimately, achieve long-term success.