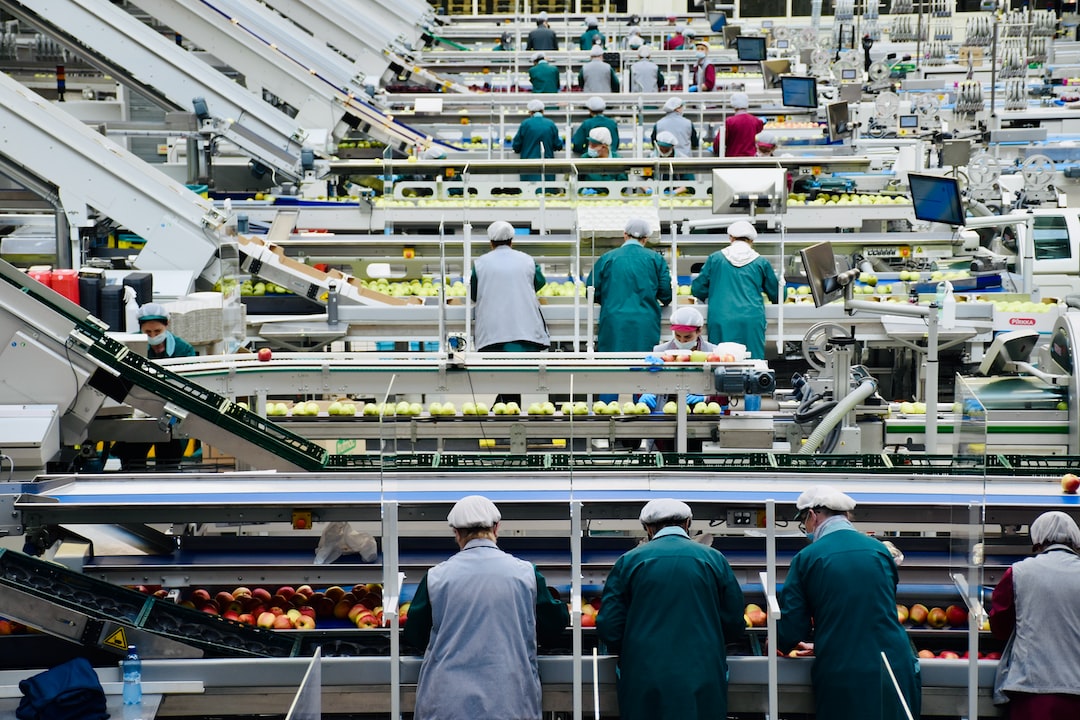
How to Optimize Production for Cost Reduction
Share0In the increasingly competitive business landscape, organizations are constantly seeking ways to optimize production processes. One key objective is cost reduction, as it directly impacts the bottom line and overall profitability. By implementing effective optimization strategies, companies can streamline operations, increase efficiency, and ultimately, minimize production costs. In this blog post, we will explore some practical measures and best practices to optimize production for cost reduction.
Identify Underutilized Resources:
The first step in optimizing production costs is to identify any underutilized resources within your organization. This may include machinery, equipment, or even personnel. Conduct a thorough audit to identify areas where resources are being wasted or not utilized to their full potential. By reallocating these resources or finding alternative uses for them, you can ensure maximum utilization and reduce the need for additional expenditure on new resources.
Streamline and Automate Processes:
As technology continues to advance, automation has become an essential tool in optimizing production processes. Evaluate your current processes and identify areas where manual intervention can be replaced with automated systems or machinery. This not only reduces the chances of human error but also increases productivity and lowers labor costs. By streamlining and automating processes, you can achieve higher output levels while using fewer resources, thus reducing costs.
Implement Lean Manufacturing Techniques:
Lean manufacturing is a philosophy aimed at minimizing waste and maximizing value in production processes. By eliminating non-value-added activities and improving efficiency, organizations can significantly reduce production costs. Some key lean principles include just-in-time (JIT) production, continuous improvement, and total quality management. Implementing these techniques not only saves time and resources but also enhances product quality, customer satisfaction, and ultimately, the profitability of the business.
Optimize Inventory Management:
Inventory management plays a crucial role in cost reduction. Excess inventory ties up capital, increases storage costs, and often leads to obsolescence. On the other hand, insufficient inventory can result in production delays and missed sales opportunities. Optimizing inventory levels through careful demand forecasting, supplier collaboration, and efficient replenishment processes can lead to significant cost savings. By maintaining a lean inventory, companies can minimize carrying costs and free up capital for other investments.
Invest in Employee Training and Development:
Employees are the backbone of any organization, and their knowledge and skills greatly impact production efficiency. Investing in training and development programs for employees can enhance their expertise, boost productivity, and improve overall process efficiency. By continuously improving the skills of your workforce, you can establish a culture of innovation, problem-solving, and continuous improvement, leading to long-term cost reductions and enhanced competitiveness.
Monitor and Analyze Performance Metrics:
To optimize production for cost reduction, it is important to regularly monitor and analyze performance metrics. Key performance indicators (KPIs) such as production output, cycle time, labor productivity, and scrap rates provide valuable insights into the efficiency and effectiveness of production processes. By tracking and analyzing these metrics, organizations can identify bottlenecks, inefficiencies, and areas for improvement. This data-driven approach enables companies to make informed decisions, implement targeted improvements, and achieve cost reduction objectives.
Collaborate with Suppliers:
Supplier collaboration is a strategic approach that can lead to substantial cost reductions in production. Engage in open and transparent communication with suppliers to negotiate better pricing, establish long-term partnerships, and explore innovative cost-saving solutions. By working closely with suppliers, organizations can identify opportunities for joint process improvements, bulk purchasing discounts, and reduced lead times. Collaborative relationships with suppliers can contribute to a more efficient and cost-effective production process.
In conclusion, optimizing production for cost reduction is an ongoing process that requires a combination of strategic planning, technology adoption, process improvement, and employee engagement. By identifying underutilized resources, streamlining processes, implementing lean manufacturing techniques, optimizing inventory management, investing in employee training, monitoring performance metrics, and collaborating with suppliers, organizations can achieve significant cost savings while enhancing efficiency, quality, and competitiveness. Embracing these optimization strategies may very well be the key to staying ahead of the competition in today’s dynamic business environment.