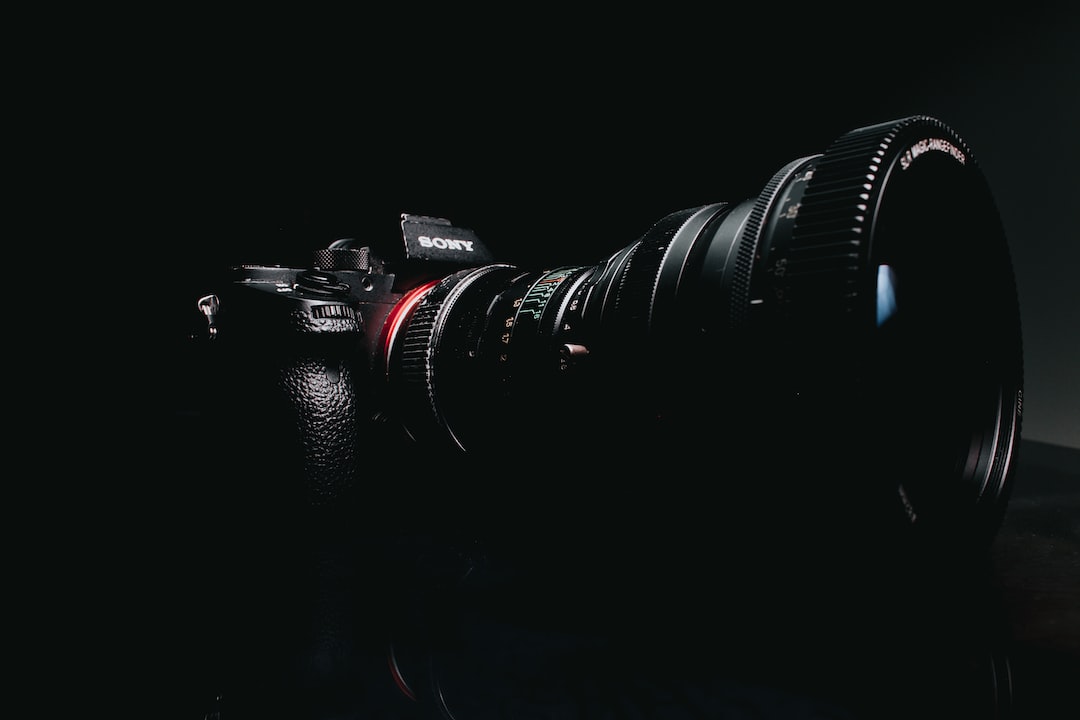
Maximizing Equipment Efficiency: Maintenance Tips for Smooth Production Operations
Share0Maximizing Equipment Efficiency: Maintenance Tips for Smooth Production Operations
In the manufacturing industry, equipment plays a crucial role in ensuring smooth operations and maintaining high production efficiency. However, over time, the performance and efficiency of any machinery can decline if not properly maintained. This can lead to costly downtime, decreased productivity, and even safety hazards. Thus, implementing effective maintenance strategies is essential for maximizing equipment efficiency and ensuring uninterrupted production.
Regular inspections and preventive maintenance are key elements in keeping machinery running smoothly. By taking a proactive approach, maintenance teams can identify and address potential issues before they become major problems. Here are some maintenance tips to help organizations maintain the highest level of equipment efficiency.
1. Create a maintenance schedule:
Developing a well-defined maintenance schedule is the foundation for efficient machinery upkeep. Designate specific inspection and maintenance periods for each piece of equipment, depending on factors such as usage frequency, hours of operation, and manufacturer’s recommendations.
2. Train maintenance personnel:
Ensure that your maintenance team is properly trained on equipment procedures, safety guidelines, and specific maintenance tasks. Well-trained technicians can efficiently diagnose and fix issues, reducing downtime and increasing overall equipment efficiency.
3. Clean and lubricate regularly:
Dust, debris, and other contaminants can cause friction, leading to increased wear and tear on machinery. Regular cleaning of equipment surfaces and components, as well as proper lubrication, can help minimize friction, reduce energy consumption, and extend the lifespan of your machinery.
4. Monitor vibration levels:
Excessive vibration is often a precursor to equipment failure. Use vibration monitoring tools to regularly check the vibration levels of critical machinery components. By identifying abnormal patterns, maintenance personnel can take timely action to address potential issues and prevent major breakdowns.
5. Keep accurate maintenance records:
Maintaining comprehensive records of all maintenance activities is critical for tracking the performance and history of your equipment. These records can help identify recurring issues, track equipment lifespan, and serve as a valuable resource for troubleshooting.
6. Implement predictive maintenance:
Utilizing sensor technologies and data analytics, predictive maintenance can anticipate equipment failures before they occur. By monitoring factors like temperature, pressure, and usage patterns, organizations can schedule maintenance tasks based on actual equipment condition rather than following a fixed schedule, reducing unnecessary downtime and optimizing equipment efficiency.
7. Train equipment operators:
Proper equipment handling and operating techniques can have a significant impact on equipment efficiency and lifespan. Train operators on best practices, including optimal starting and stopping procedures, equipment load limits, and avoiding unnecessary stress on machinery. Well-trained operators can help prevent equipment misuse and ensure the longevity of your assets.
8. Regularly calibrate equipment:
Calibration is essential in maintaining equipment accuracy and precision. Regularly calibrating instruments and measurement tools helps ensure precise readings, preventing errors and ensuring consistent quality in the production process.
9. Conduct regular audits:
Periodic audits of equipment performance and maintenance processes can help identify areas for improvement. Analyze maintenance costs, downtime patterns, and overall equipment effectiveness (OEE) to identify opportunities for increasing efficiency. Additionally, audits can help identify any non-value-added maintenance tasks that can be eliminated, saving time and resources.
10. Plan for equipment upgrades:
Technology advancements and changing production demands may require upgrading or replacing outdated machinery. Develop a strategic plan for equipment upgrades to ensure seamless transitions and avoid disruptions to production. Regularly evaluate the performance and efficiency of existing equipment to determine the need for upgrades.
By implementing these maintenance tips, organizations can optimize equipment efficiency, improve overall productivity, and reduce unexpected downtime. By taking a proactive approach and investing in regular maintenance, manufacturers can ensure that their operations run smoothly and maximize the lifespan of their machinery. Remember, prevention is always better than cure, and proper maintenance is the key to achieving optimal equipment efficiency.